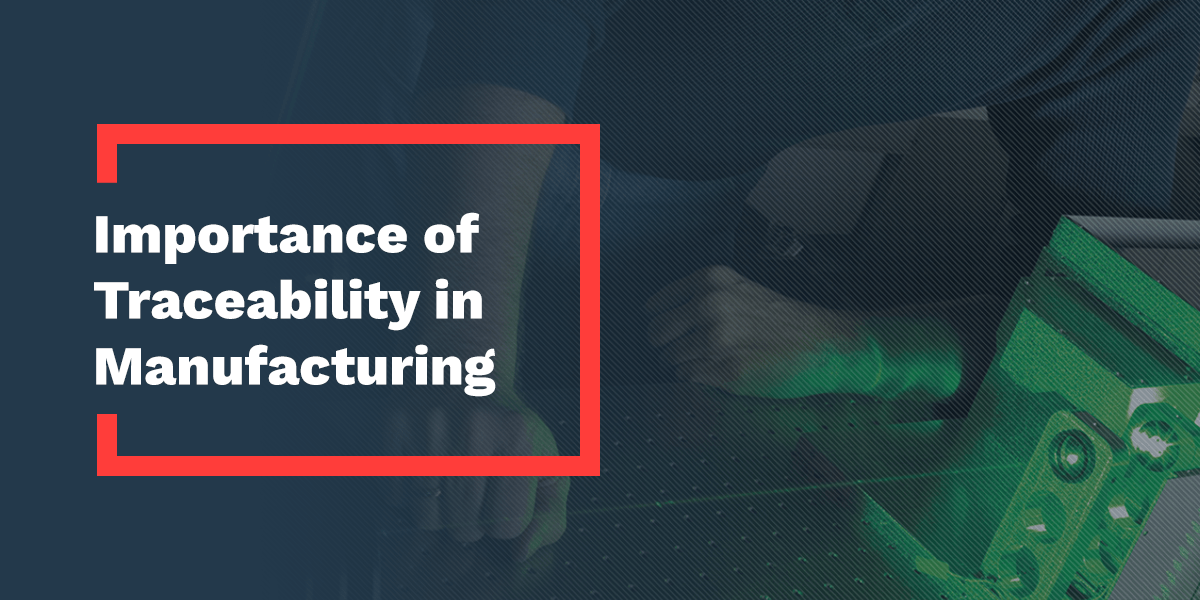
08 May Importance of Traceability in Manufacturing
Traceability in manufacturing is the ability to track and trace every aspect of the production and distribution process. It involves creating a detailed paper trail of a product’s lifecycle from sourcing raw materials to production, distribution and disposal of products. With traceability, everyone in the supply chain, down to the consumers, can tell where, when and by whom a product was produced.
It’s becoming an increasingly important part of manufacturing owing to the rise in safety awareness and consumerism. As a result, today, traceability is applicable in many industries, including food production, aerospace, automotive and medical device manufacturing. The ability to trace and track products provides businesses with real-time visibility and improves production efficiency, among other benefits discussed below.
Challenges the Manufacturing Industry Faces With Products
Many businesses in the manufacturing industry have product parts that require identifying marks to authenticate and ensure easy tracking. Failure to mark product parts during the production process results in numerous problems, including:
- Product recalls: These happen when manufacturers request the return of defective or unsafe products or batches from consumers.
- Product counterfeiting: It’s a form of consumer fraud where fake or unauthorized replica products make it to the market. Without traceability solutions, it’s challenging to authenticate products to ensure the safety of consumers and safeguard your company’s reputation.
- Product tampering: It’s the intentional or malicious alteration or contamination of a product after manufacturing. It’s a criminal offense often committed to blackmail a company, drive away customers or damage your brand’s reputation.
- Quality issues: Without traceability, manufacturers may find it difficult to standardize processes and produce quality products consistently.
How Traceability Solves Challenges in the Manufacturing Industry
Traceability provides manufacturers with information about suppliers, distributors, manufacturing notes and inspection results. This information improves the manufacturing process, enhances product quality and minimizes product damage. Here are some ways traceability helps to solve supply chain challenges in the manufacturing industry:
- Improves recall management: Traceability makes it faster and easier for manufacturers to locate products on the supply chain and recall them in due time before they cause harm to consumers. The ability to trace everything, including the quality of raw materials, also prevents avoidable recalls by ensuring you stop problems before they get to products.
- Ensures compliance: Traceability ensures regulatory compliance with local and international standards such as ISO 9001, which dictates the need to consistently manufacture products that meet customer and regulatory requirements. The food production industry has the most stringent traceability requirements. However, other industries, including automotive, aerospace and defense, also have traceability requirements that necessitate direct equipment part marking.
- Controls quality: Traceability ensures high-level quality control as manufacturers monitor and trace every step of the production process and implement effective quality control measures promptly. You can easily identify where a product quality problem may occur and resolve this before it’s passed down to the consumers.
- Prevents fraud: Implementing traceability solutions, such as direct part marking, reduces the instances of product counterfeiting and tampering because every product or batch can be authenticated and verified as it moves along the supply chain.
- Improves customer satisfaction: Robust traceability systems help to optimize customer satisfaction by ensuring manufacturers provide customers with high-quality products consistently.
- Increases transparency: Traceability enhances operational efficiency and optimizes production processes by introducing transparency on the production line. It shows the best and worst performing processes making it possible to make changes that improve manufacturing lead times.
Specific Traceability Requirements
Traceability involves two main processes — tracking and tracing. Tracking is the process of following the movement and determining the destination of a product from the point of manufacturing to the final point of distribution. On the other hand, tracing involves collecting and managing a product’s history throughout the supply chain. While tracking provides information about a product’s forward movements, tracing looks back.
To merge the two distinct components of traceability, you need a traceability system. These systems have mechanisms set to identify, link, record, store, verify and assess product information at different points of the the supply chain. They document all quality-relevant data across all the stages of production and the supply chain to prevent production errors and improve product and process quality.
Another important element of traceability in manufacturing processes is assigning every product, lot or batch with unique identification numbers, such as barcodes or 2D matrix numbers. The identification numbers are used to relay information on product dimensions, inspection results, production timelines and serial numbers.
Direct part marking is the only definitive way to ensure permanent traceability, even with heavy use. Laser marking systems, dot peen markers and scribe markers are some of the reliable permanent marking systems that produce very high-quality, high-contrast permanent marks on a variety of products and equipment parts.
How Telesis’s Traceability Solutions Can Help
Telesis supplies dot peen equipment and laser marking systems that help manufacturers in numerous industries create permanent marks and track products at different stages of the supply chain. We customize our laser and dot peen systems to meet our client’s most challenging needs, including ensuring error-free marking and meeting strict cycle times.
Our permanent marking equipment is built to last and withstand the most challenging environments, including dirt, heat and high vibrations in steel plants and the high throughput of automotive plants. Additionally, Telesis has the widest array of PINSTAMP® markers and a custom-engineered laser that you can use for serial number marking.
Here are three ways Telesis traceability solutions can help you serial numbers onto products and equipment parts:
- Stamping: This is a dot-peen marking technique that uses a pneumatically or electronically controlled pin or stylus to indent materials, often metal, and create permanent marks.
- Laser etching: It uses a high-energy laser beam to melt and expand the surface of a material and leave permanent raised marks.
- Laser marking: It uses a laser beam to remove the surface of a material to create high-contrast marks that withstand harsh conditions. Laser engraving is slower than other laser marking options but produces durable results on a wide variety of materials.
Browse Laser Markers for Manufacturing
Laser markers are essential tools in helping you achieve full traceability in manufacturing. At Telesis Technologies, we have a variety of custom laser marking and engraving machines to achieve power and precision in all your unique and demanding projects.
We develop turnkey solutions that are usable for a wide range of manufacturing industries, including food production and packaging, medical device manufacturing, automotive and aerospace. If you’re ready to purchase your high-quality laser markers today, request a quote or contact us for more information on our traceability solutions.