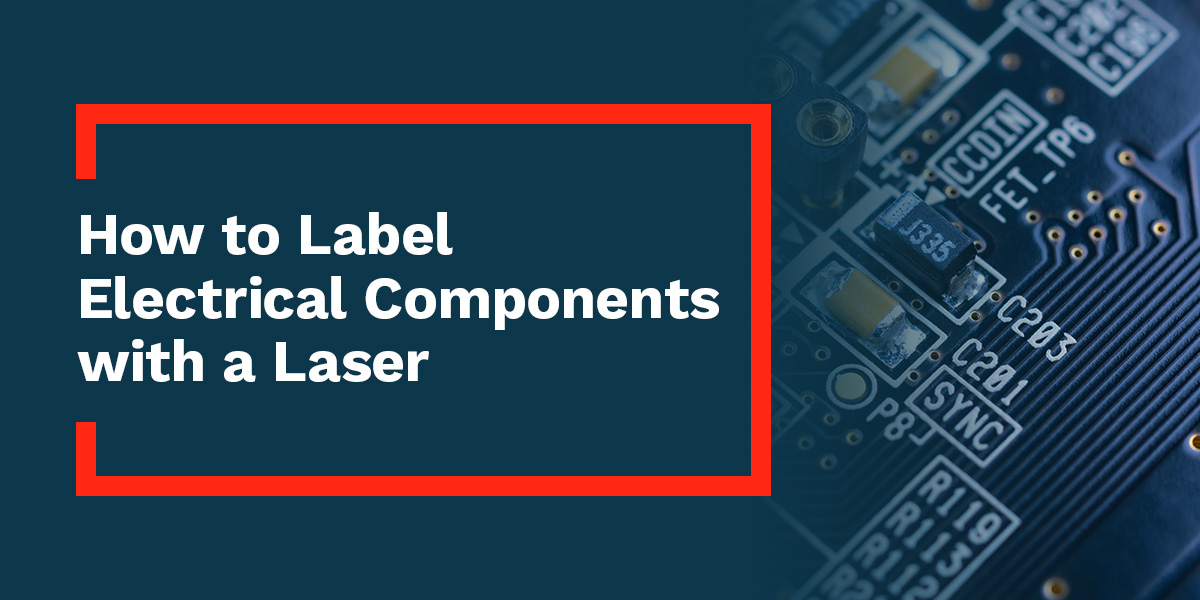
09 Feb How to Label Electrical Components With a Laser
Using a Laser Marking System to Label Electronics
Typically, manufacturers need to label electrical components with a variety of information. The items are often very delicate and small, requiring special care and specific equipment. Laser marking systems are a great way to achieve permanent labeling on silicon, plastic, metal, and other materials. Electrical components use a very wide range of materials from high temperature plastics to most metals. Lasers can cover this full range of materials and can give a range of different marks depending on the settings and type of laser.
Why Laser Technology Is the Smart Choice
The advantage of laser engraving or marking is that the mark is permanent, clean and modern. Benefits of using laser technology include:
- Durability: Laser marking uses advanced technology, allowing the markings to be durable and resistant to fading, chipping and friction. Environmental factors like chemicals, heat and sunlight also don’t have an impact.
- Precision: Laser marking allows for highly detailed and precise work. This allows for very fine text, complex logos and even intricate patterns on small components. There is also no risk of smudging, as the mark is created in the material.
- Speed: With no drying time, you can use the component immediately — there is no further processing needed. Production times for multiple components are reduced, increasing production.
- Material: Lasers can mark metals, plastics, ceramics and various other materials. They can also mark thick, thin or sensitive materials, depending on the type of laser you use and how you configure it.
- Applicable in various industries: Laser marking systems are also specially designed to fit industry needs. In the electronics industry, ultraviolet laser marking systems are the equipment of choice because they can apply a mark without any heat, protecting the integrity of the part. You can use a UV laser on printed circuit boards (PCBs), where the laser mark even becomes solder-resistant.
Types of Marks That Lasers Can Make
Electronics may require 2D matrix codes, company logos, assembly information, customer instructions or other content. You can achieve every one of these marks by utilizing a laser marking system. Often, you can apply these marks at very high speeds, resulting in fast throughput. Some other types of labeling include:
- High contrast: These are highly detailed schematics that give clear instructions for the user. You can alter the use of the laser for coloration or texture to create easily readable marks.
- Micro-engraving: Create incredibly small micro-marking on the smallest components. This accommodates the limited space on the part without compromising the integrity.
- Placement: Precise indicator marks allow for exact placement, both on a flat part or a rounded part’s circumference.
- Marking during fabrication: Mark wire insulation on the fly as you are fabricating it to streamline operations.
- Engraving: Laser engraving removes material from the surface to create a deep, permanent mark. This method is often used for marks that must withstand harsh conditions or handling. As the engraving is done with a laser, the removal of the material does not affect structural integrity or functionality.
- Etching: If a laser slightly melts the surface, this is called etching. It requires less energy and works well on many different materials, from metal to plastic. It can be used in combination with engraving to create contrast.
Establish Next-Generation Quality Control
Marking every part allows quality control and traceability of your products. With lasers, you can mark parts without physical contact, without disrupting the surface and with ultimate precision. Telesis lasers have accurate precision to mark an entire pallet of parts — in the exact location every time.
Other Benefits of Using Lasers
Laser marking provides low-cost, environmentally friendly marking compared to other forms of marking. The reason for this is:
- No waste from cartridges
- No waste from labels
- No waste from chemical solvents
In many cases, the laser is faster, has higher quality, is more accurate, offers more options and can have a return on investment in a short period of time.
Lasers offer a no-contact process. Nothing physically touches the components, resulting in less risk of contamination in sensitive or delicate components. It also allows for flexibility in labeling different materials and shapes.
The Permanent Marking and Traceability Experts
Telesis Technologies, Inc. provides the best solutions in the industry for all electrical markings. With a lineup of laser options that can mark any material and can offer powerful ultra-deep marking at the same time as delicate, cold marking. Telesis is your partner. Purchase your equipment or connect with us today.